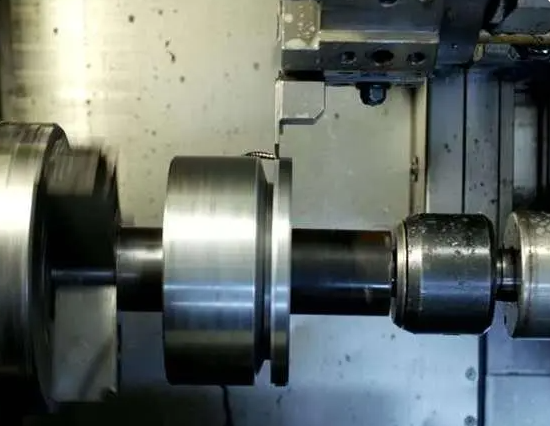
随着科技的发展,机械在人们生活中出现的频率越来越高,人们生活的各领域都有数控技术的应用。与普通车床相比较数控车床在加工精度、作业效率、自动化程度等方面具有明显的优势。随着数控技术的发展,对零件加工精度的要求也越来越高。在实际加工生产中,数控机床还不能完全发挥它的性能,在高精度工件加工上还存在许多不足,想要满足人们对工件加工的精度要求,就需要弄清楚影响数控车床加工精度的因素,并针对这些因素做出相应的优化方案[1]。
1、概述
1.1数控车床的工作原理
在普通车床的机床本体基础上加入CNC系统(计算机数字化控制系统)形成一种新的车床就是数控车床,其融合了多项先进科学技术,具有加工精度高、作业效率高、自动化程度高等优点,目前已经广泛应用于机械加工行业。数控车床的工作原理与传统车床不同,它是通过数控设备对实际要加工零件进行描述和编织语言,传输到计算机控制系统中去,再进行操作,该流程通过数字传输设备、CNC装置、控制面板等去完成,其工作过程为:工作人员先将待加工零件装置在机床本体的卡具上;工作人员将待加工零件需要加工的要求(加工形状、尺寸和精度等)通过控制面板输入到CNC系统中;工作人员在CNC系统中绘制出零件需要加工的信息(刀具移动轨迹及其他相关信息);以上信息通过CNC装置转化为代码记录在程序中,之后再传输到数控系统中[2];传输到控制系统中的信息通过PLC系统进行译码和运算,然后传出指令,下发给电气回路、主轴伺服装置及其他辅助装置等;CNC系统中的各装置将带动机床进行工作(依据之前录入和转化的数据),从而加工出符合要求的零件。
1.2数控车床的特点
与传统机床相比较数控车床加入了CNC系统,在各方面工作中数控车床零件加工具有明显优势。主要体现在四点:①加工精度高。数控车床在传统车床的基础上加入了CNC控制系统,该系统的精准度很高,可以为机械零件加工提供稳定性和一致性保障。②加工深度高。CNC控制系统可以通过汇编多种程序实现多个坐标联动的功能,因此可以加工出形状更加复杂的机械零件[3]。③提高工作效率。该系统可以通过改变输入程序去控制不同的加工零件,这种系统可以节省零件的计算评估时间,从而提高工作效率。④自动化程度高。数控车床加工零件的效率时传统车床的好几倍,其自动化程度高,在零件加工上能够批量进行,提高了工作效率减少了工作人员的工作强度。
2、影响数控车床加工精度的因素
2.1伺服系统
伺服系统可以精准的跟随或复制车床工作的某一过程,因此还被称为随动系统、反馈控制系统等,是整个数控车床系统的中枢系统。车床的零部件加工工作就是伺服系统通过驱动机床部件来完成的,而零件的加工精度也是由伺服系统控制的(由其自身的电机驱动丝杠的传动精度决定)。在实际的加工工作中,数控车床多使用闭环控制伺服进给系统,该系统在传递信号之后丝杠会发生反向运转,从而会出现短时间的空转状况。空转状况会引起反向间隙误差,进而会对零件加工精度造成影响[4]。
2.2刀具参数
数控车床通过程序控制的刀具对零件进行加工完成产品的切削。在实际工作中,切削棒料零件的车刀轴线不是固定的,会产生一定程度的变化,从而导致刀尖圆弧半径变大,切削产品的偏差也就越大。这些变化会导致轴线尺寸变大、车床刀的主偏角变小等。如果这些偏差不被及时纠正,就会导致偏差越来越严重。因此,在CNC控制系统中设置刀具参数时,要实事求是,在遵循轴向尺寸变化规律的基础上设定合理的轴向位移长度、刀尖圆弧半径和主偏角等全面分析车刀的各项参数[5]。在进行程序编程之前要清楚待加工产品的特性,对刀具轴线偏差进行科学的分析与修正,从而完成理想的零件加工。
2.3切削用量的选择
切削速度、切削深度和进给量这三者被称为切削三要素,即切削用量;这三个因素直接影响到零件加工的精度和表面粗糙程度。在零件加工的初级阶段,大多选择较大的背吃刀量来提高效率,但是背吃刀量越大切削力就越大,这种切削用量容易造成刀具和零件的损坏,对产品的加工精度造成很大的影响。在零件的精加工阶段,对工件的精度要求更加严格,所以该阶段要选择较快的切削速度和较小的进给量,同时还要根据实际的背吃刀量预留出适当的精度余量。
3、数控车床加工精度的优化方案
3.1误差改进方法
误差对数控机床加工产品的精度具有很大的影响,想要提高加工产品的精度,就一定要善于利用误差补偿法,即在系统的补偿功能基础上,天富用户注册将软件和硬件进行有机结合,补偿已经存在的坐标轴,以此来提高加工零件的精度。如果在半闭环伺服系统中出现误差问题,最好的解决办法是使用反向偏差补偿法来消除潜在误差和提高定位精度。反向偏差补偿法与误差补偿法是不同的,它是在机床工作过程中,尽量缩减零件的误差和潜伏误差,把总的误差缩减在一个可控的范围内,如图2所示为半闭环控制系统工作原理[6]。但是,该方法与误差补偿法相比费用较高,因此,还需要不断的创新与发展,以求达到低成本、低误差、高精度的加工过程。图2半闭环控制系统工作原理
3.2重视对车床机控的维护
数控车床的工作原理是通过内置的CNC控制系统对信息进行加工处理,通过变换程序和主轴更换刀具完成产品的加工,属于机电一体化产品。因此,机床需要时常进行检查,在重要部位进行油位和润滑,同时还需要定期进行滤网清理、精度调整等工作。而且,数控车床不宜长时间闲置,该机床是通过计算机进行控制的,与电气系统和机床系统有着密切关联,如果长时间没有作业,系统的插头接触、电池等容易出现问题,再次使用时可能需要进行更换才能正常工作。
3.3抑制伺服系统的误差
伺服系统是整个数控车床系统的中枢系统,在车床加工中具有重要的作用,它出现问题后会直接影响到工件加工的精准度[7]。因此,在数控机床的工作过程中一定要重视伺服系统的误差问题。可以从以下两个方面进行优化:从车床开始的设计环节就要引起重视,驱动装置要采用动态性能好的,良好的动态性能可以增强伺服装置的抗压水平和、抗载能力等,尽可能的缩减了伺服系统产生的误差可能性;伺服装置设置好之后,要对CNC控制系统的参数进行进一步的优化。
3.4防止热变形误差
随着现代制造业的发展,生产制造业对机床加工的精度要求也越来越高,而影响数控车床质量的一天富用户注册个重要因素之一就是热加工。在机床工作过程中,当工件的精准度越高时,往往受热误差的影响越高。热误差是由机床的零部件轴承和马达由于工作受温或者其他零部件的摩擦接触所产生的,同时机床零部件的摩擦会导致周围部件产生变形。我国现代制造业相对于发达国家来说发展缓慢,人们对数控机床的热误差认识不够,因此在日常生产中多会出现热误差。想要减少热误差的产生,就要从控制热源开始,可以通过建造冷却回路来控制温差,减少热量的产生和传播。
3.5优化床身导轨的几何精度
随着科学技术发展,数控车床的加工精度和效率都得到了改善。数控车床的性能和机构也随着科技的发展在进一步的更新,同时也对车床底座铸件的重量、导轨精度等提出了更高的要求。主要表现在以下两个方面:全新的数控车床需要更加灵活的斜床造型来支撑,传统的复杂铸件无法完成;企业要确保数控车床运行的稳定性,不断提高数控车床的抗弯水平和抗扭水平。
4、结语
随着科学技术的发展,数控车床加工技术的应用也越来越广泛,生产制造业对机床加工的精度要求也越来越高,零件加工的精度与质量受数控车床技术的多方面影响[8],相对于普通车床技术来说,在精度和质量上已经有所提高。但是,数控车床技术在工件精度加工方面还存在一些问题,只有将这些影响车床加工零件精度的因素抑制住,才可以提高数控车床加工技术的精度和质量,从而提高企业在市场中的竞争力,促进企业经济增长